
Oil Separators : Larger Tonnage and Commerical Systems
Oil separators serve a critical function in many systems.
Regardless of the type of compressor, oil will leave with the discharge
gas. This oil must be separated from the high pressure gas and returned
to the compressor. Minimizing oil circulation improves system operating
efficiency by improving the heat transfer characteristics of the evaporator
and condenser. It also ensures that adequate oil is available for essential
compressor lubrication.
Typically, Oil separators operate on the principle of slowing the velocity of oil laden discharge gas. This slowing is accomplished by the internal design of the separator that either utilizes an abrupt change of direction, internal baffling, impingement screens or large openings of the piping at the entrance of the separator.
Oil is usually mixed with the hot discharge gas in the form of a fog. This oil / refrigerant fog mixture hits the screens or baffles and slows down rapidly, causing fine particles of oil to hit each other and form larger particles that, with the help of fine mesh impingement screens, are separated from the refrigerant and collect in the reservoir at the bottom of the seperator housing.
We have included an animated simulation of the A-F Oil Separator.
Click on this link to view this interactive exercise:
A-F Oil Separator Simulation
A small float will rise when the reservoir oil level reaches a determined level. The rising float opens a needle valve that allows the oil to return to the compressor crankcase through a small oil return line. Oil is forced thru the return line due to the pressure difference between the high side location of the separator and the low side compressor crankcase.
Another design that provides a very high oil separation efficiency is the Centrifugal or Helical Oil Separator. The discharge oil / refrigerant fog enters the separator and hits the leading edge of a helical path. The fog mixture is centrifugally forced along this spiral path. Oil is forced to the edge of the path and collects , then runs down onto impingement screen layers that further separates and drains to the reservoir for return, via the float / valve back to the compressor.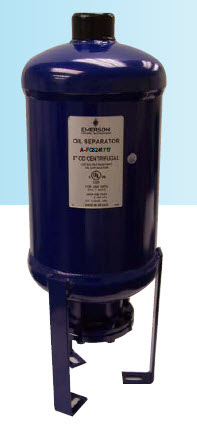
Parallel rack systems benefit from the most efficient oil separators.
Emerson Climate Technologies™ has optimized a centrifugal oil separator
for just these applications. The oil separator captures more than 99% of
oil. This directly results in energy savings due to reduced time between
loading of the evaporator and reduced compressor work.
The graph illustrates that the Emerson® oil separators are more than
twice as efficient as other leading models in removing oil from
circulation. An additional benefit is a lower pressure drop in all tests,
which reduces compressor work, thereby extending the life of the
compressor. The larger oil separators are also serviceable, helping to
facilitate routine maintenance.
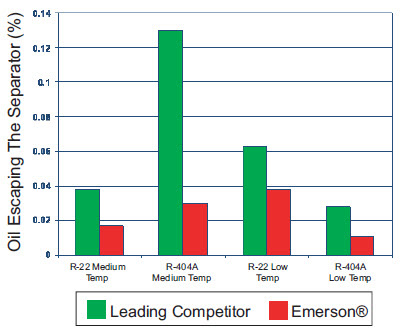
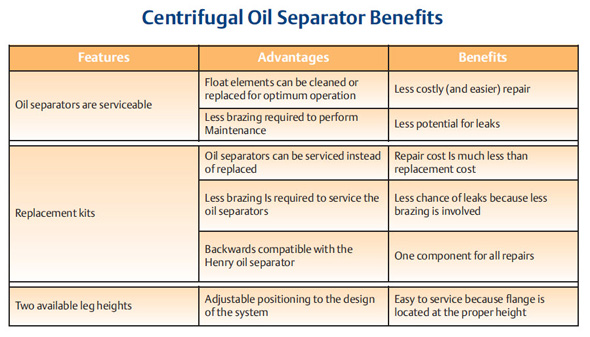
An Oil Separator needs to be maintained at a warm temperature to prevent refrigerant from condensing to a liquid during the off cycle. The float valve can't distinguish between liquid refrigerant and oil. If liquid refrigerant collects and returns to the compressor crankcase, this would dilute the oil and cause compressor lubrication problems. If this transfer of liquid refrigerant through the oil return line is occurring, the line will be cold from vaporizing refrigerant experiencing the pressure drop.
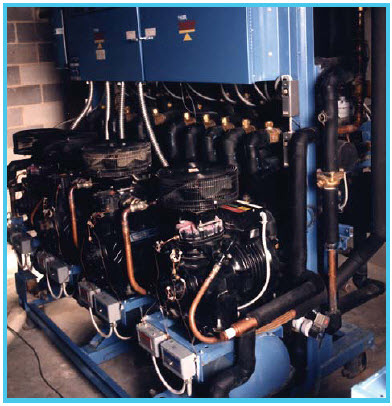
A damaged, leaking or collapsed float in the separator will result in a high level of oil in the reservoir, causing low lubricant levels in the crankcase, which may end in damage to the compressor.
Copyright © Blue C LLC. All rights reserved. |